The Science Behind Porosity: A Comprehensive Overview for Welders and Fabricators
Comprehending the elaborate systems behind porosity in welding is vital for welders and producers making every effort for impeccable craftsmanship. As metalworkers explore the midsts of this phenomenon, they uncover a world controlled by different variables that influence the formation of these tiny gaps within welds. From the make-up of the base materials to the complexities of the welding procedure itself, a plethora of variables conspire to either intensify or minimize the presence of porosity. In this thorough overview, we will untangle the scientific research behind porosity, exploring its impacts on weld top quality and introduction progressed techniques for its control. Join us on this journey through the microcosm of welding imperfections, where precision satisfies understanding in the quest of remarkable welds.
Comprehending Porosity in Welding
FIRST SENTENCE:
Assessment of porosity in welding exposes essential insights right into the integrity and high quality of the weld joint. Porosity, characterized by the presence of dental caries or spaces within the weld metal, is a typical concern in welding procedures. These voids, if not properly attended to, can jeopardize the structural integrity and mechanical residential or commercial properties of the weld, causing potential failings in the completed item.

To find and quantify porosity, non-destructive testing techniques such as ultrasonic testing or X-ray evaluation are often used. These techniques enable the identification of interior defects without endangering the stability of the weld. By examining the dimension, shape, and circulation of porosity within a weld, welders can make enlightened choices to boost their welding processes and attain sounder weld joints.
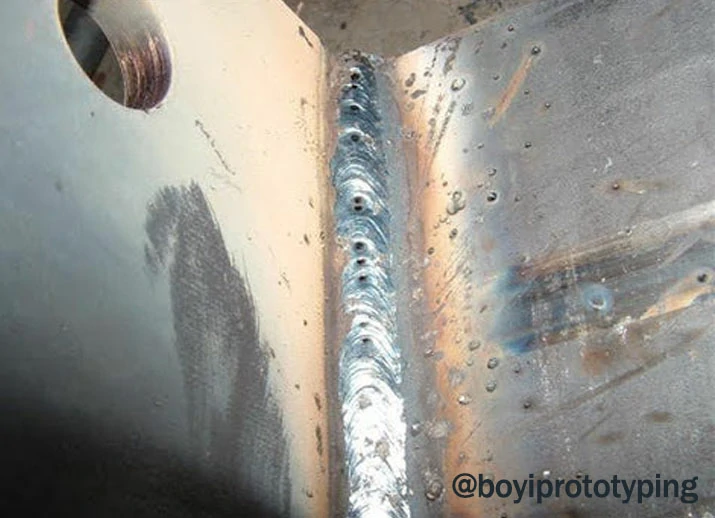
Factors Affecting Porosity Formation
The event of porosity in welding is affected by a myriad of elements, varying from gas shielding performance to the complexities of welding parameter setups. Welding specifications, including voltage, existing, travel speed, and electrode type, also effect porosity formation. The welding strategy used, such as gas metal arc welding (GMAW) or secured steel arc welding (SMAW), can influence porosity development due to variations in warm circulation and gas read this protection - What is Porosity.
Results of Porosity on Weld Quality
The visibility of porosity also weakens the weld's resistance to rust, as the entraped air or gases within the spaces can react with the surrounding setting, leading to destruction over time. Additionally, porosity can impede the weld's ability to withstand pressure or impact, further threatening the total high quality and dependability of the bonded framework. In critical applications such as aerospace, auto, or structural constructions, where safety and longevity are vital, the detrimental effects of porosity on weld high quality can have extreme effects, highlighting the significance of minimizing porosity through proper welding methods and treatments.
Methods to Decrease Porosity
Additionally, using the appropriate welding specifications, such as the proper voltage, present, and take a trip rate, is important in avoiding porosity. Keeping a constant arc length and angle during welding additionally helps minimize the possibility of porosity.

Using the appropriate welding method, such as back-stepping or utilizing a weaving activity, can additionally assist disperse warm evenly and decrease the possibilities of porosity formation. By carrying out these strategies, welders can effectively lessen porosity and create top quality welded joints.

Advanced Solutions for Porosity Control
Applying innovative technologies and ingenious techniques plays an essential role in accomplishing remarkable control over porosity in welding processes. One advanced option is the usage of innovative gas mixes. Protecting gases like helium or a mixture of argon and hydrogen can help in reducing porosity by offering far better arc stability and improved gas insurance coverage. Additionally, utilizing advanced welding strategies such as pulsed MIG welding or customized atmosphere welding can also aid minimize porosity issues.
Another sophisticated solution involves making use of sophisticated welding equipment. Utilizing devices with built-in functions like waveform control and innovative power resources can enhance weld high quality and decrease porosity dangers. The implementation of automated welding systems with precise control over criteria can substantially minimize porosity issues.
Moreover, including innovative surveillance and examination modern technologies such as real-time X-ray imaging or automated ultrasonic testing can help in spotting porosity early in the welding process, view publisher site enabling for prompt corrective actions. In general, integrating these sophisticated services can greatly boost porosity control and improve the general quality of welded components.
Final Thought
In verdict, recognizing the scientific research behind porosity read this article in welding is vital for welders and fabricators to create high-grade welds. By determining the factors influencing porosity development and applying strategies to decrease it, welders can enhance the overall weld top quality. Advanced options for porosity control can further boost the welding procedure and make sure a solid and reliable weld. It is essential for welders to continually enlighten themselves on porosity and carry out ideal techniques to attain optimum results.
Comments on “What is Porosity in Welding: Usual Sources and Effective Solutions”